게시판
Force balance (Servo) Sensor
작성자
newgeovan
작성일
2018-07-29 13:05
조회
1421
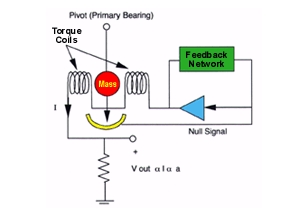
Force-balance (Servo) Sensors
The force-balance accelerometer is shown below where a
pendulous, high-magnetic permeability mass is hung from
a hinge as shown. The "down" or "null position" is detected
by the null detector and the counterbalancing force is provided
by a magnetic coil.
The Servo Accelerometer
If acceleration is applied to this assembly, a force is exerted on
the mass and it will attempt to move from the null position.
When the null detector detects motion, the coil current is increased
by means of a servo amplifier to maintain the null position.
The coil current provides the restoring force required to maintain
the null position and this current will be in direct proportion to the
applied acceleration.
Highly-precise null detectors can be easily fabricated as the total
range of this deflection is extremely small, in fact, increasing null
detector resolutions will result in proportionately improved
acceleration resolution. Since the active member of the force-balance
accelerometer does not substantially displace in normal operation,
the hysteresis performance of this type of sensor is extremely low
and is due more to electrical hysteresis in the circuitry than to actual
mechanical hysteresis. Damping of the seismic assembly is
accomplished both electrically and mechanically with silicone oil.
The servo accelerometer is physically large relative to strain-gage
accelerometers but provides microgravity resolution with high
zero-hertz stability and low thermal errors. The large size of the
inertial mass results in large forces during high shock events,
and even though overrange-ilmiting stops may be incorporated,
this type of sensor is not suited to high shock ebvironments.
Early force balance sensors were provided with piezoelectric
or magnetic "dithering" mechanisms to reduce stiction effects
by constantly oscillating the bearing slightly to keep the coefficient
of bearing friction in the lower dynamic range. Recent designs,
utilizing high-resolution null detect systems, eliminate the bearing
altogether replacing it with a simple quartz flexure. The superb
mechanical characteristics of crystalline quartz, used as a pivot,
provides essentially-zero hysteresis performance due to the fact
that the mass does not deflect significantly.
The typical useful flat (±5%) frequency response bandwidth of
the servo accelerometer is generally less than 100 Hertz.
Based upon a closed-loop control network, recovery time of a
servo accelerometer from an overrange input can be lengthy
relative to the strain-gaged open-loop accelerometer designs.
In fact, the recovery time of the sensor, after an over-ranged input,
is a direct function of the total power available to the restoring force
mechanism. Typical force balance sensors are usually current-limited
to 50 or 100 ma of input drive current thus "energy limiting" the
restoring force mechanism resulting in typical overrange recovery
times of 100 milliseconds.
The large thermal mass of this sensor type renders the device
reasonably insensitive to thermal transients.
The Servo or Force-balanced Pressure Sensor
The diagram shows how the servo force-balance concept
can be applied to fabricate extremely-high-precision pressure
sensors based upon the above concepts. The force-balance
pressure sensor is generally large, and typically not suited to
dynamic pressure measurements or physically-hostile
environments, but is admirably suited to the high-precision
and high-resolution measurement of pressure in more benign
physical environments.
전체 0